In today’s healthcare landscape, ensuring that every medical device operates reliably isn’t just about efficiency—it’s a matter of patient safety. Effective maintenance practices underpin the operational success of healthcare facilities and contribute significantly to cost efficiency. Yet, many medical devices fall short of expectations due to inadequate maintenance. For example, data from the WHO Medical Device Technical Series (Source: who) reveals that nearly half of the medical devices in low-income countries are non-operational because of poor maintenance. This startling statistic highlights the critical need for medical device maintenance best practices that can ensure devices are always in peak condition.
Medical device maintenance best practices are essential for manufacturers, as they not only impact patient care but also affect the bottom line. Regular, proactive maintenance ensures that devices remain reliable over time and minimizes unexpected breakdowns that can disrupt hospital operations. Moreover, investing in proper maintenance leads to significant savings over the long term by reducing costly repairs and extending the lifespan of expensive equipment. This is where cost management in medical device maintenance plays a vital role. Manufacturers need to strike a balance between robust maintenance protocols and cost-effective operations.
One key aspect of these practices is the integration of design for maintainability in medical devices. This approach encourages manufacturers to build devices that are not only innovative but also easy to maintain. By incorporating maintainability during the design phase, manufacturers can ensure that routine repairs and updates are streamlined, reducing both downtime and maintenance costs. It’s about creating products that are as user-friendly for maintenance teams as they are effective in patient care.
Compliance with evolving regulations is another crucial component. Medical devices must adhere to strict standards to be safe and effective. Adhering to compliance with maintenance regulations for medical devices ensures that manufacturers not only meet legal requirements but also build trust with healthcare providers. These regulations, outlined in guidelines such as those provided by AAMI , set the benchmark for quality and safety, urging manufacturers to maintain high standards in every aspect of device upkeep.
In addition to robust design and regulatory compliance, ongoing education is vital. Implementing comprehensive training programs for medical device maintenance equips technicians with the latest skills and knowledge needed to manage sophisticated equipment. These programs ensure that maintenance teams are proficient in troubleshooting, repairing, and even performing predictive maintenance for medical equipment. Predictive maintenance leverages modern technologies like AI and IoT to forecast equipment failures before they happen, which can drastically reduce downtime and further cut costs.
To summarize, enhancing maintenance in the realm of medical equipment manufacturing is multifaceted. It involves adopting medical device maintenance best practices, focusing on design for maintainability in medical devices, ensuring compliance with maintenance regulations for medical devices, and investing in effective training programs for medical device maintenance. Additionally, embracing technologies that enable predictive maintenance for medical equipment plays a crucial role in maintaining uninterrupted service and managing costs effectively.
The goal of this blog is to guide manufacturers through these best practices, offering actionable insights and evidence-based strategies to optimize maintenance routines. By understanding and applying these principles, manufacturers can ensure that their devices remain reliable, safe, and cost-efficient—ultimately leading to better patient outcomes and enhanced operational performance.
Understanding Maintenance Requirements
When it comes to medical equipment, robust maintenance isn’t a luxury—it’s an absolute necessity for ensuring patient safety, device reliability, and cost efficiency. For manufacturers, implementing medical device maintenance best practices means embracing a comprehensive approach that covers different types of maintenance and adhering to strict regulatory standards. In this section, we’ll break down the three main types of maintenance—preventive, corrective, and predictive—and explore the regulatory frameworks that guide them, including FDA, ISO, and CMS guidelines. This understanding is essential for achieving effective cost management in medical device maintenance and ensuring compliance with maintenance regulations for medical devices.
Types of Maintenance
- Preventive Maintenance
Preventive maintenance involves scheduled inspections and routine servicing designed to keep equipment running optimally before problems arise. This type of maintenance is proactive and centers on tasks like regular cleaning, calibration, and part replacement. By adhering to a planned schedule, manufacturers can minimize unexpected breakdowns and extend the lifespan of their devices. For instance, routine calibration of diagnostic devices not only improves their accuracy but also reduces the frequency of emergency repairs. Incorporating design for maintainability in medical devices during the product development phase can further streamline these preventive processes by making devices easier to service.
Key activities in preventive maintenance include:
- Scheduled Inspections: Regularly examining equipment to catch early signs of wear and tear.
- Routine Servicing: Cleaning, lubricating, and calibrating devices according to manufacturer guidelines.
- Documentation: Keeping detailed records of all maintenance activities to support quality control and regulatory audits.
- Corrective Maintenance
Corrective maintenance, on the other hand, is a reactive strategy employed when a device fails or malfunctions. This approach focuses on identifying the root cause of an issue and implementing repairs to restore functionality. While corrective maintenance is crucial for addressing unexpected equipment failures, relying solely on this approach can lead to higher costs and increased downtime. It is therefore important to integrate corrective measures with preventive strategies to ensure a balanced and sustainable maintenance regimen.
Key elements of corrective maintenance include:
- Rapid Response: Quickly addressing equipment failures to minimize downtime.
- Troubleshooting: Diagnosing issues accurately to prevent recurrence.
- Repair and Replacement: Efficiently fixing or replacing faulty components to restore device operation.
- Predictive Maintenance
Predictive maintenance for medical equipment represents a cutting-edge approach that leverages data analytics, sensor technology, and the Internet of Things (IoT). By continuously monitoring equipment performance, predictive maintenance can forecast potential failures before they happen. This not only minimizes unplanned downtime but also allows for maintenance to be scheduled exactly when needed, leading to more efficient resource allocation and better cost management in medical device maintenance. Manufacturers employing predictive strategies can adjust their maintenance schedules based on real-time data, ensuring devices operate at peak performance.
Key benefits of predictive maintenance include:
- Data-Driven Insights: Utilizing real-time data to anticipate and address potential issues.
- Optimized Maintenance Schedules: Shifting from fixed schedules to condition-based maintenance, reducing unnecessary servicing.
- Cost Savings: Lowering repair costs by preemptively addressing issues before they escalate.
A Comparative Overview
Below is a summary table that outlines the key differences and benefits of each maintenance type:
Type of Maintenance | Key Activities | Benefits |
Preventive | Scheduled inspections, routine cleaning, calibration | Reduces unplanned downtime, extends device lifespan |
Corrective | Troubleshooting, repairs, component replacement | Restores functionality quickly after failure |
Predictive | Data analytics, sensor monitoring, trend analysis | Minimizes unexpected failures, optimizes resource use, reduces costs |
Regulatory Standards and Compliance
Adhering to regulatory standards is fundamental for ensuring that maintenance practices meet stringent quality and safety benchmarks. For example, the FDA’s Quality System Regulation (source: FDA) outlines the necessary protocols for maintaining medical devices. Compliance with these guidelines is a critical element of compliance with maintenance regulations for medical devices.
Other key regulatory frameworks include:
- ISO Standards: These provide international benchmarks for quality management and maintenance practices in medical device manufacturing.
- CMS Guidelines: The Centers for Medicare & Medicaid Services offer additional regulations that influence how maintenance programs should be structured, especially in hospital settings.
- The Joint Commission Standards: These emphasize maintaining a safe environment for patient care by ensuring that equipment is consistently monitored and maintained. More details can be found at (Source: jointcommission).
Integrating these regulatory standards into maintenance practices ensures that manufacturers not only follow medical device maintenance best practices but also build trust with healthcare providers and regulatory bodies.
Integrating Training and Technology
To effectively implement these maintenance strategies, manufacturers should also invest in robust training programs for medical device maintenance. Continuous education and training ensure that maintenance teams are updated on the latest techniques, regulatory changes, and technological advancements. This can include hands-on training sessions, workshops, and certification programs, which collectively enhance the overall quality of maintenance.
Moreover, integrating advanced technologies plays a pivotal role in modern maintenance strategies. For instance, using IoT sensors and predictive analytics for predictive maintenance for medical equipment allows for real-time monitoring and early detection of potential issues. This technological integration not only supports better maintenance practices but also contributes significantly to cost management in medical device maintenance by preventing expensive emergency repairs.
Final Thoughts
Understanding and balancing preventive, corrective, and predictive maintenance is essential for establishing comprehensive medical device maintenance best practices. By adhering to regulatory standards and investing in training and technology, manufacturers can enhance device reliability, ensure patient safety, and achieve significant cost savings over time. As the industry evolves, the ability to adapt maintenance strategies in line with emerging technologies and updated regulations will be key to long-term success.
This approach not only supports better compliance with maintenance regulations for medical devices but also reinforces the overall efficiency and reliability of medical equipment—an essential goal for every manufacturer committed to excellence in the healthcare sector.
By integrating these maintenance requirements into daily operations, manufacturers can ensure their equipment remains safe, reliable, and cost-efficient, paving the way for sustained excellence in medical device performance.
Designing for Maintainability in Medical Devices
Creating medical devices that are easy to maintain is not just a technical challenge—it’s a strategic advantage. In today’s competitive market, manufacturers are increasingly focusing on design for maintainability in medical devices as a core element of their product development. By integrating design principles like modularity, standardization, and accessibility early in the process, manufacturers can significantly reduce maintenance time, lower operational costs, and improve overall device reliability.
One of the fundamental aspects of design for maintainability in medical devices is modularity. Modular designs allow individual components or subsystems to be replaced or upgraded without having to overhaul the entire device. This not only accelerates repair times but also simplifies routine maintenance tasks. For example, a modular imaging system can have its sensor or processing unit replaced independently, ensuring that the device remains operational with minimal downtime. Studies on maintainability from (Source: Sciencedirect ) support the idea that modularity can drastically reduce repair time and contribute to medical device maintenance best practices.
Standardization is another key principle that aids maintainability. By standardizing components, manufacturers create uniformity across different product lines. This means that maintenance teams can quickly identify and source replacement parts, streamlining repair processes. Standardized designs also contribute to cost management in medical device maintenance by reducing inventory complexity and lowering procurement expenses. In addition, standardized systems tend to simplify training, making training programs for medical device maintenance more efficient and effective.
Accessibility is a critical yet sometimes overlooked design factor. Devices that are designed with clear access points for critical components enable easier inspections, cleaning, and repairs. By ensuring that all parts are reachable without the need for specialized tools or excessive disassembly, manufacturers can facilitate faster service turnaround times and enhance overall service efficiency. This approach not only supports medical device maintenance best practices but also contributes to better compliance with maintenance regulations for medical devices, as easier access helps meet regulatory requirements for regular inspections and servicing.
To put these principles into perspective, consider the following summary of design elements and their benefits:
Design Principle | Key Benefits |
Modularity | Quick component replacement, reduced downtime, simplified upgrades |
Standardization | Uniformity across devices, reduced inventory costs, streamlined training |
Accessibility | Easier inspections and repairs, faster service times, improved compliance |
By embracing these design principles, manufacturers not only create products that are easier to maintain but also lay the groundwork for incorporating advanced strategies like predictive maintenance for medical equipment in the future. When devices are designed with maintainability in mind, data from routine servicing can be more effectively leveraged to predict potential failures and plan preventive actions—thus contributing to cost management in medical device maintenance.
Moreover, integrating maintainability into the design phase is a proactive measure that ensures long-term reliability and customer satisfaction. It aligns with the broader scope of medical device maintenance best practices by reducing the frequency and impact of equipment failures. Manufacturers who prioritize these design elements are better positioned to meet evolving regulatory standards, adapt to technological advances, and ultimately deliver superior products in the healthcare sector.
ISO Standards, accessible at ISO, further reinforce the importance of a structured approach to design. By aligning with ISO guidelines, manufacturers can ensure that their devices not only perform efficiently but also adhere to global quality benchmarks, solidifying their reputation as leaders in innovation and reliability.
Training and Certification
For medical equipment manufacturers, ensuring that maintenance staff are highly skilled and certified is essential to uphold medical device maintenance best practices. Trained technicians not only perform routine tasks more effectively but also contribute to overall cost management in medical device maintenance by reducing downtime and expensive emergency repairs. One of the most recognized certifications in the field is the CBET (Certified Biomedical Equipment Technician) certification offered through AAMI Training Programs for Medical Device Maintenance . This certification, along with other continuous education programs, ensures that maintenance professionals are well-prepared to tackle the challenges of modern medical equipment.
Why Training Matters
Effective training programs for medical device maintenance are critical because they empower technicians with the knowledge and skills to handle sophisticated medical devices. With rapid technological advancements, the complexity of medical equipment continues to increase, making it imperative for technicians to stay updated on new diagnostic tools, repair techniques, and safety protocols. This continuous learning environment not only supports medical device maintenance best practices but also reinforces the importance of compliance with maintenance regulations for medical devices. For instance, regulatory bodies such as the FDA and ISO demand that maintenance procedures are executed by individuals who understand the nuances of advanced equipment, ensuring that repairs and routine maintenance adhere to strict quality standards.
Key Elements of Effective Training
Training programs in the medical device maintenance arena typically cover a broad spectrum of topics, including:
- Fundamentals of Medical Device Operation: Understanding how devices function and the principles behind their design is critical. This foundational knowledge helps technicians diagnose issues more accurately.
- Hands-on Skill Development: Practical experience is indispensable. Training programs often include lab sessions where technicians can practice repairs and preventive maintenance on actual devices.
- Regulatory and Safety Standards: Continuous education on regulatory requirements, such as those outlined in the FDA’s Quality System Regulation (Source: FDA), ensures that technicians understand compliance with maintenance regulations for medical devices.
- Advanced Diagnostic Tools: As medical equipment becomes more sophisticated, training often incorporates the use of advanced diagnostic tools and techniques, including those for predictive maintenance for medical equipment. This helps in identifying issues before they lead to major failures.
Certification Programs and Continuous Education
The CBET certification is a prime example of how formal credentials can significantly enhance a technician’s capabilities. Accredited by AAMI Training Programs, the CBET program equips technicians with the skills necessary to perform a wide range of maintenance tasks, from routine inspections to complex repairs. Achieving such certification not only boosts individual competence but also elevates the overall standard of maintenance operations within a manufacturing facility.
Moreover, continuous education is a vital component of sustaining excellence in the maintenance field. With technological innovations constantly emerging, training is not a one-time event but an ongoing process. Manufacturers are increasingly investing in periodic refresher courses, workshops, and webinars that help their maintenance teams stay at the forefront of industry developments. This commitment to lifelong learning ensures that technicians can adapt to new challenges, thereby supporting cost management in medical device maintenance by preemptively addressing potential issues.
Impact on Operational Efficiency
Well-trained technicians contribute significantly to smoother operations and improved device uptime. When maintenance teams are adept at both routine and emergency repairs, the likelihood of prolonged equipment downtime decreases markedly. This proactive approach aligns perfectly with medical device maintenance best practices, as it minimizes the disruptions that can affect patient care and overall facility efficiency.
Furthermore, effective training supports the integration of emerging technologies, such as predictive maintenance for medical equipment. By combining hands-on training with data analytics, technicians can leverage real-time insights to foresee and prevent equipment failures. This not only enhances device reliability but also optimizes maintenance schedules, thereby reducing operational costs.
In summary, robust training and certification programs are indispensable for medical equipment manufacturers. They ensure that maintenance teams are not only well-versed in current technologies and repair methods but also fully compliant with regulatory standards. By investing in training programs for medical device maintenance and fostering a culture of continuous education, manufacturers can safeguard their equipment’s reliability, enhance operational efficiency, and maintain a competitive edge in the healthcare industry.
Implementing Effective Field Service Management
In the complex world of medical equipment maintenance, effective field service management (FSM) is the cornerstone of ensuring devices remain operational, safe, and cost-efficient. Manufacturers who embrace robust FSM practices can significantly enhance their medical device maintenance best practices. By streamlining scheduling, dispatching, technician management, customer communication, and parts inventory management, organizations not only minimize downtime but also drive overall efficiency and cost management in medical device maintenance.
Efficient Scheduling and Dispatching
A well-organized scheduling system is critical for reducing equipment downtime. By automating job assignments and real-time dispatching, manufacturers can ensure that maintenance teams respond promptly to issues, preventing minor faults from escalating into major failures.
- Optimized Scheduling:
Implementing a dynamic scheduling system helps balance workload and prioritize urgent repairs. An efficient schedule minimizes gaps and redundancies, ensuring that maintenance tasks are carried out swiftly. This approach supports medical device maintenance best practices by reducing the frequency of emergency repairs and optimizing technician time. - Real-Time Dispatching:
Modern FSM solutions enable real-time tracking of service calls. With instant notifications and mobile access, technicians can be dispatched immediately, ensuring that no call for service is missed. This transparency not only boosts team responsiveness but also reinforces predictive maintenance for medical equipment, as trends in service calls can highlight recurring issues.
Case studies from the Journal of Clinical Engineering demonstrate that organizations leveraging real-time scheduling and dispatching report up to a 30% reduction in equipment downtime, leading to enhanced operational efficiency.
Technician Management and Training
Managing a highly skilled technician workforce is vital. Beyond simply dispatching jobs, effective field service management includes ongoing support, training, and performance monitoring.
- Training Programs for Medical Device Maintenance:
Investing in continuous education is essential. Programs like those offered through AAMI Training Programs ensure that technicians remain current with evolving technologies and regulatory requirements. These training programs for medical device maintenance not only improve service quality but also empower technicians to execute advanced repair techniques. - Certification and Skill Development:
Certifications such as CBET (Certified Biomedical Equipment Technician) validate a technician’s proficiency. Such credentials are crucial for building a competent maintenance team that adheres to compliance with maintenance regulations for medical devices. Continuous skill development, supported by structured training programs, can directly impact the quality and speed of service. - Performance Monitoring:
Effective technician management also involves tracking performance through key metrics. Regular reviews and feedback sessions help identify areas for improvement and foster a culture of continuous learning. This process, when integrated into FSM, ensures that technicians consistently follow medical device maintenance best practices.
Enhancing Customer Communication
In the realm of healthcare, transparent and proactive communication with customers is as important as the technical execution of maintenance tasks. Clear communication channels help build trust and keep all stakeholders informed about service statuses and anticipated resolutions.
- Proactive Updates:
Automated communication systems can notify customers and facility managers about upcoming maintenance schedules, expected downtime, and service completion times. This level of transparency minimizes frustration and builds confidence in the maintenance process. - Feedback Loops:
Incorporating customer feedback is vital for continuous improvement. By actively soliciting feedback after service calls, manufacturers can fine-tune their processes and address any recurring issues, thereby reinforcing medical device maintenance best practices. - Digital Platforms:
Using customer portals or mobile apps to track service progress in real time further enhances the customer experience. These platforms enable quick access to maintenance records, upcoming service reminders, and even predictive alerts about potential equipment issues, aligning with predictive maintenance for medical equipment strategies.
Parts Inventory Management
Managing spare parts inventory is a critical component of field service management. An efficient parts management system ensures that technicians have the right parts available when needed, reducing service delays and preventing prolonged equipment downtime.
- Streamlined Inventory Systems:
Automated inventory tracking systems can monitor stock levels in real time and forecast parts usage based on historical maintenance data. This proactive approach is integral to cost management in medical device maintenance, as it prevents overstocking while ensuring that essential parts are always on hand. - Integration with FSM:
Integrating parts inventory management with FSM systems allows for seamless order processing and restocking. For instance, when a maintenance request is logged, the system can automatically check the inventory for required components and trigger a restock order if needed. This integration supports medical device maintenance best practices by ensuring that inventory shortages do not delay repairs. - Case Studies and Best Practices:
Research and case studies, such as those highlighted in ManageEngine FSM Best Practices, show that effective inventory management can reduce repair times by up to 25%. This significant improvement not only boosts service efficiency but also contributes to overall cost management in medical device maintenance.
Integrating Technology and Data Analytics
Modern FSM solutions leverage technology to integrate scheduling, dispatching, technician management, and inventory control into one unified system. By using data analytics and IoT devices, organizations can further enhance their maintenance strategies.
- Predictive Analytics:
Predictive maintenance for medical equipment is greatly enhanced by data analytics. By analyzing data from previous service records, usage patterns, and sensor readings, the system can forecast potential failures before they occur. This proactive measure ensures that maintenance interventions are timely, reducing both downtime and repair costs. - Unified Dashboard:
A unified FSM dashboard provides a holistic view of all maintenance activities, from scheduled tasks to real-time service calls and inventory status. This transparency allows managers to make informed decisions and adjust strategies dynamically, ensuring adherence to medical device maintenance best practices. - Compliance and Reporting:
Integrating data analytics also facilitates compliance with regulatory requirements. Detailed reports generated by the FSM system can be used during audits to demonstrate adherence to compliance with maintenance regulations for medical devices. This not only helps in meeting legal standards but also reassures customers and regulatory bodies about the reliability of maintenance operations.
Best Practices for Implementing FSM
To implement effective field service management, manufacturers should consider the following best practices:
- Adopt an Integrated FSM Platform:
Ensure that your FSM system integrates scheduling, dispatching, technician management, and inventory tracking into a single platform. This consolidation helps in maintaining a clear overview of all operations and improves response times. - Invest in Continuous Training:
Regularly update your maintenance staff through comprehensive training programs for medical device maintenance. A well-trained team is better equipped to handle advanced diagnostics and repairs, ensuring that your FSM practices remain robust and effective. - Utilize Real-Time Data:
Leverage IoT sensors and data analytics for predictive maintenance for medical equipment. This approach not only minimizes unexpected failures but also contributes to efficient cost management in medical device maintenance. - Enhance Communication Channels:
Implement digital tools that facilitate real-time communication between maintenance teams and customers. Transparent communication helps manage expectations and improves customer satisfaction. - Regularly Review and Update Processes:
Continuously assess your FSM practices against industry benchmarks and case studies, such as those provided by the Journal of Clinical Engineering and ManageEngine FSM Best Practices. Regular reviews ensure that your processes evolve in line with technological advancements and regulatory changes.
Implementing effective field service management is essential for enhancing medical device maintenance best practices. By focusing on efficient scheduling, real-time dispatching, comprehensive technician management, proactive customer communication, and streamlined parts inventory management, manufacturers can create a robust maintenance ecosystem. This ecosystem not only supports cost management in medical device maintenance but also paves the way for integrating predictive maintenance for medical equipment—ensuring that medical devices remain reliable, compliant, and ready to deliver top-notch performance.
The benefits of a well-implemented FSM system are clear: reduced downtime, lower operational costs, improved service quality, and greater customer satisfaction. In an industry where every minute counts and patient safety is paramount, investing in a holistic FSM approach is not just beneficial—it’s imperative.
Leveraging Technology
In today’s rapidly evolving healthcare landscape, technology plays a pivotal role in transforming maintenance operations for medical equipment. Leveraging advanced field service management (FSM) software, IoT, and data analytics not only optimizes maintenance routines but also lays the groundwork for superior medical device maintenance best practices. By integrating these technological solutions, manufacturers can streamline processes, reduce downtime, and achieve significant cost management in medical device maintenance.
The Power of FSM Software
Modern FSM software automates many of the manual tasks that previously slowed down maintenance operations. With an integrated system that covers scheduling, dispatching, technician management, customer communication, and parts inventory, FSM software provides a single platform for managing all aspects of maintenance. Here’s how it makes a difference:
- Automated Scheduling and Dispatching:
FSM software optimizes maintenance schedules by automatically assigning jobs based on urgency, technician availability, and location. This dynamic scheduling reduces idle time and ensures that service calls are addressed promptly, a core component of medical device maintenance best practices. Automated dispatching also allows for real-time tracking of service requests, ensuring transparency and accountability across teams. - Centralized Technician Management:
By maintaining detailed profiles and performance metrics, FSM software helps managers assign tasks to the most qualified technicians. This centralized approach enables better coordination and faster turnaround times, directly impacting cost management in medical device maintenance. In addition, when integrated with training programs for medical device maintenance, FSM software ensures that technicians remain updated on the latest procedures and compliance requirements. - Efficient Parts Inventory Management:
An effective FSM system tracks inventory levels in real time, ensuring that essential parts are always in stock. By automating reordering processes and using historical maintenance data to forecast future needs, manufacturers can prevent delays and avoid overstocking—further enhancing cost management in medical device maintenance.
These integrated features not only lead to smoother operations but also enable healthcare providers to adhere strictly to compliance with maintenance regulations for medical devices. The result is a system that supports proactive maintenance and minimizes the risks of unexpected equipment failures.
Better maintenance starts with better tools. Try FieldAx for free for one month and see how effortless medical equipment management can be!
Harnessing the Internet of Things (IoT)
IoT technology has revolutionized how manufacturers monitor and maintain medical equipment. With smart sensors and connectivity, IoT devices enable continuous, remote monitoring of equipment performance, delivering data that is critical for timely interventions.
- Remote Monitoring and Real-Time Alerts:
IoT devices embedded within medical equipment can monitor vital parameters and alert maintenance teams when deviations occur. For example, if a sensor detects unusual vibration levels or temperature fluctuations, it can trigger an alert for preventive maintenance. This real-time monitoring is essential for predictive maintenance for medical equipment, ensuring that potential failures are addressed before they escalate into costly repairs. - Enhanced Data Collection:
The continuous stream of data provided by IoT devices offers valuable insights into the operating conditions of medical equipment. This data can be analyzed to identify trends and patterns, thereby enabling manufacturers to make informed decisions about maintenance scheduling and equipment upgrades. With robust data at their fingertips, organizations can improve medical device maintenance best practices by basing their actions on real-world performance metrics. - Improved Equipment Uptime:
By leveraging IoT, manufacturers can ensure that equipment remains in optimal condition, ultimately reducing downtime and enhancing service reliability. This connectivity not only supports the principles of design for maintainability in medical devices but also reinforces overall operational efficiency.
Overall, IoT technology is a game changer in the maintenance space. It transforms traditional reactive maintenance models into proactive strategies, ensuring that medical devices are consistently performing at their best.
The Role of Data Analytics in Predictive Maintenance
Data analytics is the cornerstone of modern maintenance strategies, particularly when it comes to predictive maintenance for medical equipment. By analyzing data collected from FSM software and IoT sensors, manufacturers can predict when a device is likely to fail and schedule maintenance accordingly. This proactive approach not only prevents costly breakdowns but also optimizes resource allocation.
- Predictive Analytics in Action:
Using sophisticated algorithms, data analytics can detect early signs of potential issues. For example, a study published in Frontiers in Public Health (Source: frontiersin) on predictive maintenance in Malaysia demonstrated how data-driven insights can forecast equipment failures. By identifying patterns and anomalies in performance data, manufacturers can act before a minor issue becomes a major disruption. This strategy is a key pillar of predictive maintenance for medical equipment, reducing emergency repairs and enhancing overall service quality. - Maintenance Prioritization:
Data analytics helps prioritize maintenance tasks by assessing the severity and likelihood of equipment failure. IntechOpen Maintenance Prioritization (Source: intechopen) provides a framework for ranking maintenance needs based on critical factors such as device usage, age, and historical performance. By applying these insights, organizations can allocate their resources more effectively, ensuring that the most critical equipment receives attention first. This approach is integral to both medical device maintenance best practices and cost management in medical device maintenance. - Improved Decision-Making:
With access to detailed analytics, managers can make better-informed decisions regarding maintenance schedules, parts ordering, and technician assignments. Predictive analytics not only reduces the risk of unexpected downtime but also aligns with the strategic goals of medical device maintenance best practices by supporting evidence-based decision-making.
Integration of Technology: Overcoming Challenges and Maximizing Benefits
While the benefits of leveraging FSM software, IoT, and data analytics are substantial, integrating these technologies is not without its challenges. Successful implementation requires careful planning, investment in training, and a commitment to continuous improvement.
- Integration Challenges:
One of the primary challenges is ensuring that different technology systems—such as FSM software, IoT platforms, and analytics tools—can seamlessly communicate with each other. Data silos, incompatible software, and inadequate IT infrastructure can hinder the integration process. Manufacturers must invest in robust IT solutions and foster cross-department collaboration to overcome these obstacles. - The Importance of Training:
To fully leverage technology, it’s crucial that maintenance teams are well-trained on how to use these tools. Training programs for medical device maintenance become even more important in this context, as technicians must be proficient not only in traditional maintenance techniques but also in operating advanced digital systems. Continuous training ensures that staff can maximize the benefits of FSM software, IoT, and data analytics, thereby driving overall improvements in maintenance efficiency. - Best Practices for Implementation:
- Conduct a Technology Audit: Start by assessing the current state of your maintenance processes and IT infrastructure. Identify gaps and determine which areas would benefit most from technological enhancements.
- Develop an Integration Roadmap: Create a detailed plan for integrating FSM software with IoT devices and analytics platforms. This roadmap should include milestones, resource allocation, and timelines for deployment.
- Invest in Training and Support: Ensure that your team has access to comprehensive training programs for medical device maintenance. Regular workshops, webinars, and on-site training sessions can help bridge the knowledge gap.
- Monitor and Adjust: Once the system is in place, continuously monitor its performance and gather feedback from technicians. Use this information to fine-tune processes and address any issues promptly.
- Measuring Success:
Manufacturers should establish clear metrics to evaluate the effectiveness of their technology integration. Key performance indicators (KPIs) might include reduction in downtime, cost savings, and improvements in service response times. By regularly reviewing these KPIs, organizations can ensure that their technology investments are yielding tangible benefits and contributing to medical device maintenance best practices.
Real-World Impact: A Case Study Perspective
A compelling example of the power of technology in maintenance comes from a case study published in Frontiers in Public Health (Source: frontiersin). In Malaysia, healthcare providers leveraged predictive analytics to monitor critical equipment and schedule maintenance proactively. This initiative led to a notable decrease in unexpected equipment failures and significant cost savings over time. Such real-world applications underscore the transformative potential of integrating advanced technologies into maintenance operations.
Moreover, insights from IntechOpen Maintenance Prioritization (Source: intechopen) reinforce that when maintenance tasks are prioritized based on data, organizations can dramatically improve efficiency. Prioritization enables manufacturers to allocate resources to the most critical issues first, ensuring that devices are maintained according to the highest medical device maintenance best practices.
Compliance and Quality Assurance
Ensuring that maintenance meets strict regulatory standards is a cornerstone of medical device maintenance best practices. For medical equipment manufacturers, robust compliance and quality assurance protocols not only safeguard patient safety but also drive long-term cost savings through efficient cost management in medical device maintenance. In this section, we explore how regular audits, meticulous documentation, and well-defined quality control processes help manufacturers adhere to regulatory standards such as those set forth by the FDA and The Joint Commission.
The Importance of Regulatory Compliance
Regulatory standards are in place to guarantee that medical devices remain safe and reliable. The FDA Device Regulation (Source: FDA) outlines stringent guidelines that manufacturers must follow to ensure quality throughout a device’s lifecycle. Similarly, The Joint Commission (Source: jointcommission) provides comprehensive standards for maintaining an environment of care, emphasizing the need for regular maintenance and audits.
Meeting these standards is not simply about avoiding penalties; it builds trust with healthcare providers and patients alike. Compliance with maintenance regulations for medical devices is a key element of overall quality assurance. Manufacturers who rigorously follow these standards often experience fewer device failures and better overall performance, contributing to enhanced medical device maintenance best practices.
Regular Audits and Inspections
One of the most effective ways to ensure compliance is through regular audits. Audits serve as an internal checkpoint, verifying that all maintenance activities are performed according to established protocols. These audits should cover various aspects, including:
- Equipment Inspections: Regularly scheduled checks to identify potential issues before they become critical.
- Maintenance Logs: Detailed documentation of all maintenance activities, including preventive, corrective, and predictive maintenance tasks.
- Process Reviews: Evaluations of the maintenance processes themselves to ensure they align with regulatory guidelines and industry standards.
A well-structured audit process not only ensures adherence to compliance with maintenance regulations for medical devices but also helps identify areas where cost management in medical device maintenance can be improved. By catching potential inefficiencies early, manufacturers can reduce unnecessary expenditures and improve the overall reliability of their equipment.
Detailed Documentation and Maintenance Logs
Accurate documentation is critical for quality assurance and regulatory compliance. Maintaining comprehensive maintenance logs helps create a verifiable record of all servicing activities. These logs are invaluable during regulatory audits and serve as proof that medical device maintenance best practices are being followed consistently.
Key aspects of effective documentation include:
- Service Records: Every maintenance task—whether preventive, corrective, or predictive—should be logged with details about the work performed, parts replaced, and any observations noted by the technician.
- Compliance Checklists: These ensure that each device is maintained according to FDA and Joint Commission standards. Checklists also help in confirming that no critical steps are overlooked.
- Historical Data: Over time, collected data can reveal trends and inform future maintenance schedules. This historical perspective is essential for integrating predictive maintenance for medical equipment into overall maintenance strategies.
When maintenance logs are meticulously maintained, manufacturers are better prepared for audits and can quickly address any discrepancies. This proactive approach not only minimizes the risk of non-compliance but also supports cost management in medical device maintenance by reducing unexpected repairs and downtime.
Quality Control Processes
Beyond audits and documentation, having robust quality control processes in place is essential to ensure that every maintenance task meets high standards. Quality control in maintenance involves:
- Standard Operating Procedures (SOPs): Clearly defined procedures for all maintenance activities ensure consistency and reliability. SOPs serve as a roadmap for technicians and help in maintaining medical device maintenance best practices.
- Training and Certification: Ongoing training programs for medical device maintenance play a critical role in quality control. Certified technicians are better equipped to perform complex maintenance tasks and adhere to stringent quality standards.
- Performance Metrics: Establishing key performance indicators (KPIs) such as downtime reduction, repair turnaround time, and compliance rate helps manufacturers measure the effectiveness of their maintenance processes. Data from these metrics can guide improvements and ensure that quality control remains a priority.
A systematic quality control framework helps bridge the gap between regulatory compliance and everyday maintenance tasks. By ensuring that every technician follows the same high standards, manufacturers not only meet compliance with maintenance regulations for medical devices but also reinforce medical device maintenance best practices across their operations.
Cost Insights and Long-Term Benefits
Implementing stringent compliance and quality assurance measures can lead to substantial cost savings. For example, a detailed cost analysis from PMC Cost-Minimization Analysis (when available) often shows that proactive audits, detailed documentation, and rigorous quality control processes reduce the need for expensive corrective maintenance. Manufacturers that invest in these processes can avoid costly downtime, extend the lifespan of their equipment, and ultimately achieve better cost management in medical device maintenance.
Consider the following summary of benefits:
Aspect | Benefits |
Regular Audits | Early detection of issues, improved process efficiency |
Detailed Documentation | Verifiable records for audits, trend analysis, and historical insights |
Quality Control Processes | Consistent maintenance quality, reduced risk of non-compliance |
Training and Certification | Enhanced technician skills, better adherence to regulatory standards |
This holistic approach to compliance and quality assurance not only ensures that medical devices are maintained at the highest level but also creates a sustainable model for long-term operational efficiency. In an industry where patient safety and device reliability are paramount, such measures are indispensable.
Final Thoughts
In summary, achieving excellence in medical equipment maintenance requires a deep commitment to compliance and quality assurance. By implementing regular audits, maintaining detailed maintenance logs, and enforcing rigorous quality control processes, manufacturers can meet and exceed regulatory standards. These efforts support compliance with maintenance regulations for medical devices and contribute significantly to cost management in medical device maintenance.
As healthcare technology continues to evolve, integrating robust compliance measures with advanced maintenance strategies will remain critical. Manufacturers who prioritize these elements not only ensure safer, more reliable equipment but also set a strong foundation for innovation and growth in the competitive healthcare landscape.
By embedding these quality assurance and compliance strategies into daily operations, manufacturers can uphold medical device maintenance best practices while delivering dependable, high-quality healthcare solutions.
Final Insights and Future Trends
As we look ahead, it’s clear that robust maintenance strategies will continue to evolve alongside advancements in technology and shifts in regulatory landscapes. The journey to achieving medical device maintenance best practices has covered many crucial aspects—from robust maintenance types and design principles that focus on design for maintainability in medical devices, to comprehensive training programs for medical device maintenance, and effective field service management that supports predictive maintenance for medical equipment. Alongside these, strict adherence to compliance with maintenance regulations for medical devices and efficient cost management in medical device maintenance remain critical for manufacturers.
Moving forward, several emerging trends are set to redefine the maintenance landscape:
- Artificial Intelligence and Machine Learning:
The adoption of AI is transforming how maintenance schedules are determined. With AI-driven analytics, manufacturers can predict equipment failures with greater accuracy, optimizing maintenance schedules to ensure that preventive measures are implemented precisely when needed. This shift to AI-powered predictive maintenance for medical equipment will not only minimize downtime but also reduce operational costs. Market research reports indicate a significant increase in AI adoption in healthcare maintenance strategies (Source: marketsandmarkets). - Internet of Things (IoT) and Remote Monitoring:
IoT technology continues to enhance remote monitoring capabilities, enabling real-time tracking of device performance. With continuous data streams, maintenance teams can detect early signs of wear and tear, leading to timely interventions. This integration of IoT with FSM systems is a game changer, reinforcing medical device maintenance best practices and providing actionable insights that drive better cost management in medical device maintenance. - Sustainability and Eco-Friendly Practices:
Sustainability is becoming a focal point in the healthcare industry. Manufacturers are now exploring eco-friendly materials and energy-efficient designs that contribute to design for maintainability in medical devices while also reducing environmental impact. Sustainable practices not only appeal to a growing eco-conscious market but also contribute to long-term savings and operational efficiency. - Cybersecurity in Connected Systems:
As medical devices become increasingly interconnected through IoT and integrated FSM software, cybersecurity emerges as a critical concern. Ensuring the protection of sensitive data and safeguarding against cyber threats is essential for maintaining the integrity of maintenance operations. Robust cybersecurity measures must be an integral part of maintenance strategies to protect both patient safety and device functionality. - Enhanced Training and Continuous Education:
The rapid pace of technological change necessitates that technicians remain up-to-date with the latest developments. Ongoing training programs for medical device maintenance will continue to be essential. By investing in continuous education, manufacturers can ensure that their workforce is well-equipped to handle new technologies and adapt to evolving regulatory requirements.
A snapshot of future trends is illustrated in the table below:
Future Trend | Key Impact | Benefits |
AI and Machine Learning | Enhanced predictive maintenance capabilities | Reduced downtime, improved resource allocation, lower repair costs |
IoT and Remote Monitoring | Real-time equipment tracking and data collection | Timely interventions, better maintenance scheduling, cost savings |
Sustainability | Adoption of eco-friendly materials and designs | Long-term operational savings, reduced environmental impact |
Cybersecurity | Protection of interconnected systems against threats | Safeguarded data, maintained operational integrity |
Continuous Training | Ongoing education for maintenance teams | Up-to-date skills, improved service quality, adherence to regulations |
Looking forward, manufacturers who embrace these emerging trends will be better positioned to not only meet current challenges but also to lead innovation in the healthcare maintenance sector. By integrating advanced technologies with traditional medical device maintenance best practices, companies can create a resilient maintenance framework that supports both immediate operational goals and long-term strategic growth.
These future strategies underscore the importance of a holistic approach that balances technology, regulatory compliance, and human expertise. As market dynamics continue to shift, staying adaptable and proactive will be the key to achieving excellence in medical equipment maintenance. Health Facilities Management insights (Source: hfmmagazine) further highlight that integrating these advanced strategies not only improves device reliability and patient safety but also contributes significantly to overall operational efficiency and cost savings.
Embracing these innovations today sets the stage for a future where medical equipment is maintained at the highest standard, ensuring that healthcare providers can continue to deliver safe, effective, and reliable care.
Streamline your medical equipment maintenance with ease. Try FieldAx free for one month and experience seamless scheduling, tracking, and compliance management!
Author Bio
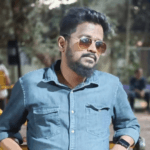
Palani Kumar
Palani Kumar is a seasoned digital marketing professional with over 13 years of experience in crafting impactful strategies for B2B brands.
As the marketing lead at FieldAx, he focuses on bridging the gap between technology and business growth, simplifying complex field service management concepts into valuable insights.
Passionate about delivering informative and practical content, Palani writes about industry trends, best practices, and innovations that help businesses optimize their field operations.
When not working on marketing strategies, he enjoys exploring history, engaging in thought-provoking discussions, and appreciating the balance between technology and tradition.